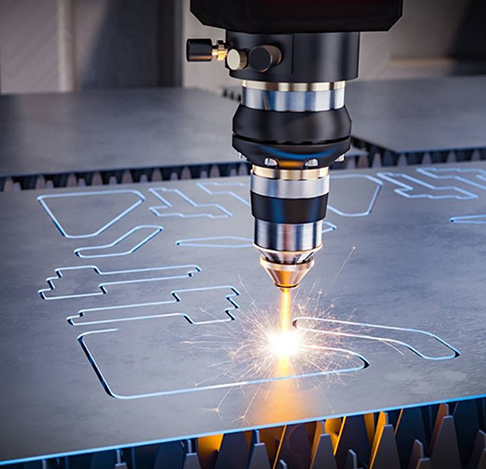
درباره ما
سری تراشی کریمان
با پیشینه افزون بر 4 دهه فعالیت موفق و حرفه ای و بهره مندی از نیروی انسانی متخصص و کارآمد ,تحقق ارزشهای مورد انتظار مشتریان را سرلوحه فعالیت خود قرار داده و امکانات و دستگاه های تمام اتوماتیک سریتراشی و سی ان سی و از تجهیزات پیشرفته و به روز جهت تولید قطعات مورد نیاز کارخانجات جهت تولید قطعات مورد نیاز با آلیاژ برنج آلومینیوم آهن از قطر دو تا شصت میلیمتر مطابق با معیارهای مورد انتظار مشتریان در خدمت صنعت کشور میباشد…
خدمات
شرح دستگاه و توانایی های این واحد صنعتی
دستگاه تراش سی ان سی CNC
سری تراشی با تراش cnc یک فرایند پیشرفته و کاربردی برای صنایع مختلف است. دستگاه تراش cnc ترکیبی از اعداد و کدها را اجرا می کند و با توجه به اینکه عملکرد دستگاه خودکار است در نتیجه موجب افزایش سرعت و دقت در تولید قطعات می شود.این دستگاه قادر است تا یک فرایند دستوری را برای دفعات زیادی به صورت دقیق اجرا کند.
تراش CNC از صنعت پزشکی گرفته تا صنایع خودروسازی و هوافضا کاربردی است. سری تراشی با تراش CNC در صنعت قطعه سازی جهان مدرن کاربرد ویژه ای دارد. این دستگاه قادر است کوچکترین قطعات را با دقت میکرون برش دهد.
دستگاه قلاویز زنی و حدیده کاری
قلاویز زنی یکی از جمله عملیاتی است که نیازمند دقت بالا در چرخش مته و سه نظام است. عمل قلاویز زدن بدون دستگاه های بادقت و با دریلهای معمولی کاملا غیر ممکن خواهد بود. دقت و قدرت بیشتر از مزایای مهم در دستگاه های تراشکاری کریمان میباشد که باعث محبوبیت و مورد توجه قرار گرفتن آن شده است. در نهایت و به عبارت بهتر، برای هر پروژه و قطعه کاری که نیازمند سوراخکاری دقیق، بدون هیچ انحراف و خطایی است و باید تمرکز در کارگیر و همچنین میزان فشار مته بر روی قطعه کاملا در اختیار کاربر باشد.که این امر نیز در مجموعه ما با دقت و سرعت بالا در حال انجام می باشد.
دستگاه های تراش تراب
دستگاه سری تراش یا تراب دستگاهی است که می تواند قطعات صنعتی قابل ماشین کاری را به طور سری و در تیراژ بالا تولید کند که به دلیل تولید اقتصادی با دقت و کیفیت بالا دستگاه تراش را در فرمها و شکلهای مختلفی میسازند و از طرفی به منظور ارزان بودن و سرعت بالای تراشکاری نسبت به سایر روشها استفاده از ماشین تراش یک روش معمول و پر استفاده در صنعت میباشد. لازم به ذکر است که تنظیم و راه اندازی این دستگاه مستلزم مهارت و تخصص خاصی میباشد تا در بازه زمانی معین به حداکثر تعداد تولیدات باکیفیت دست یافت که خوشبختانه مجموعه تراشکاری کریمان با به کارگیری نیروهای متخصص و مجرب در این زمینه زیرساخت های لازم جهت تولید قطعات با کیفیت با سرعت و دقت مثال زدنی را فراهم ساخته است.
مقالات
آخرین مقالات
مقدمه تراشکاری سیلندر یکی از رایجترین عملیاتهای ماشینکاری است که در تولید قطعات استوانهای، مانند شفتها، محورهای صنعتی، و اجزای ماشینآلات کاربرد فراوان دارد. این فرآیند به منظور کاهش ابعاد قطعه، بهبود سطح تماس، و ایجاد شکلهای خاص در سطح خارجی یا داخلی قطعه انجام میشود. انواع مختلف تراشکاری سیلندر براساس نوع عملیات و قطعه مورد نظر تقسیمبندی میشوند. در این میان، تراشکاری خارجی، داخلی، نیمهداخل و تراشکاری ویژه برای ایجاد سطحهای خاص مهمترین نوعها هستند. تراشکاری خارجی بیشتر برای سطح بیرونی قطعات استوانهای به کار میرود و نقش مهمی در تولید قطعاتی مانند میلگردها، شفتها، وُسطحههای مورد نیاز برای مونتاژ دارند. این نوع تراشکاری به کمک ابزارهای برش و دستگاههای تراش عمومی انجام میشود و در صنعتهای مختلف کاربرد دارد. تراشکاری داخلی یا درونی برای اکستنشن سطح داخلی لولهها یا محفظهها، و تراشکاری نیمهداخل برای عملیاتهایی است که به صورت همزمان سطح بیرونی و داخلی باید اصلاح شود. علاوه بر این تراشکاری ویژه برای سطحهای خاص، مانند سطحهای شیاردار یا سطحهای با مقاومت خاص، کاربرد دارد. کاربردهای تراشکاری سیلندر بسیار گسترده است، از جمله ساخت و تعمیر ماشینآلات، تولید قطعات خودرو، صنایع هوافضا، ابزارآلات صنعتی و قالبسازی. این فرآیند به تولید قطعات با دقت بالا و سطح صاف و یکنواخت کمک میکند که در نتیجه عمر مفید و کارایی قطعات افزایش مییابد. در کل شناخت انواع و کاربردهای مختلف این عملیات، برای مهندسان و تکنسینهای حوزه ماشینکاری بسیار حائز اهمیت است تا بتوانند بهترین روش را بر اساس نیاز پروژه و مشخصات قطعه انتخاب کنند. با سری تراشی همراه باشید. فرآیند تراشکاری سیلندر فرآیند تراشکاری سیلندر، یکی از پایهترین عملیاتهای ماشینکاری است که در تولید قطعات استوانهای مورد استفاده قرار میگیرد. این فرآیند با هدف برداشتن مواد اضافی از سطح قطعه، اصلاح ابعاد و شکل، و تولید سطوح صاف و یکنواخت انجام میشود. در این عملیات، قطعه موردنظر معمولاً ثابت بر روی میز ماشین قرار میگیرد و ابزار برش که معمولاً یک تیغه برنده یا یک ابزار برش مدرن است، بر روی سطح قطعه حرکت میکند تا یک سطح استوانهای دقیق و مقاوم ساخته شود. در فرآیند تراشکاری سیلندر، پارامترهای مهمی مانند سرعت دوران قطعه، تغذیه ابزار، عمق برش و نوع ابزار باید به دقت تنظیم شوند. این پارامترها بر دقت ابعادی، سطح نهایی، و عمر ابزار تاثیر مستقیم دارند. به عنوان مثال، افزایش سرعت دوران ممکن است باعث افزایش کیفیت سطح شود، اما در مقابل عمر ابزار کاهش یابد. بنابراین، تنظیم صحیح این پارامترها نیازمند دانش فنی و تجربه است. مزیت دیگر این فرآیند در امکان اصلاح یا اصلاح مجدد قطعه است که به عنوان مرحلهای مهم در فرآیندهای تولید صنعتی شناخته میشود. علاوه بر این استخدام تجهیزات مدرن و ابزارهای پیشرفته، باعث افزایش سرعت، دقت و کاهش هدررفت مواد میشود. در نهایت این فرآیند نقش مهمی در ساخت قطعات ماشینآلات، خودروسازی، هوافضا و صنایع دیگر دارد و کنترل دقیق آن منجر به تولید قطعات با کیفیت بالا و کارکرد مطمئن میگردد. همچنین بخوانید: تراشکاری صنعتی چیست؟ معرفی روشهای مختلف تراشکاری سیلندر یا استوانه تراشکاری سیلندر یا استوانه، روشهای متعددی دارد که هر کدام بر اساس نوع قطعه، نیاز دقت و سطح مورد نظر انتخاب میشود. این روشها عمدتاً به دو دسته کلی تقسیم میشوند: تراشکاری خارجی و تراشکاری داخلی. در ادامه هر کدام از آن ها پرداخته ایم: تراشکاری خارجی (External Turning) این روش معمولترین نوع تراشکاری است که بر روی سطح بیرونی قطعه انجام میشود. در این فرآیند قطعه بر روی ماشین تراش ثابت میشود و ابزار برش بر روی سطح خارجي حرکت میکند تا سطح صاف، هموار و با ابعاد دقیق ایجاد شود. این عملیات برای ساخت شفتها، میلگردها و قطعات استوانهای کاربرد دارد. تراشکاری داخلی (Internal Turning) در این روش، برعکس تراشکاری خارجی، عملیات بر روی سطح داخلی قطعه صورت میگیرد. این فرآیند برای ساخت سوراخهای دقیق، محفظهها و عملیاتهایی که به اصلاح سطوح داخلی نیاز دارند، استفاده میشود. ابزارهای مخصوص و دستگاههای خاص برای این نوع تراشکاری به کار میروند. تراشکاری نیمهداخل (Partial Turning) این روش ترکیبی است که در آن قسمتهایی از سطح بیرونی و داخلی همزمان تراش داده میشود. در مواردی که نیاز به اصلاح هر دو سطح است، از این روش بهره میبرند. تراشکاری سطح خاص (Special Surface Turning) در مواردی سطحهایی با خواص خاص مانند سطحهای شیاردار، با مقاومت بالا یا با طراحیهای خاص نیاز است که عملیات تراشکاری مخصوص انجام میشود. هر کدام از این روشها با توجه به نیازهای پروژه و نوع قطعه، بر اساس دقت، سرعت و هزینه انتخاب میشوند. در کل، آگاهی از این روشها به مهندسان کمک میکند تا عملیات مناسب را برای به دست آوردن بهترین نتیجه انتخاب کنند و کیفیت نهایی محصولات را تضمین نمایند. تراشکاری سیلندر خارجی (External Cylinder Turning) تراشکاری سیلندر خارجی یا External Cylinder Turning یکی از مهمترین و پرکاربردترین عملیاتهای ماشینکاری است که در ساخت و اصلاح قطعات استوانهای کاربرد دارد. در این عملیات، قطعه بر روی دستگاه تراش ثابت شده و ابزار برش بر روی سطح خارجی آن حرکت میکند تا سطح صاف، هموار و مطابق با ابعاد طراحی شده تولید شود. این نوع تراشکاری در بسیاری از صنایع، از جمله خودروسازی، هوافضا، قالبسازی و ماشینآلات صنعتی کاربرد دارد. در فرآیند تراشکاری خارجی، پارامترهای مهمی مانند سرعت دوران قطعه، تغذیه ابزار، عمق برش و نوع ابزار باید به دقت تنظیم شوند. تنظیمات صحیح این پارامترها نقش کلیدی در رسیدن به دقت ابعادی، سطح نهایی با کیفیت و کاهش خطاهای ماشینکاری دارند. در ضمن انتخاب نوع ابزار مانند تیغههای کارباید یا فولادی، بستگی به نوع ماده قطعه و نیازهای سطحی دارد. از مهمترین مزایای این روش میتوان به تولید سریع و دقت بالا اشاره کرد. همچنین قابلیت انجام عملیاتهای تکمیل، اصلاح و نیز تراشکاری چند مرحلهای در یک نمونه قطعه ممکن است. این عملیات برای تولید قطعاتی است که نیازمند دقت بسیار بالا، مقاومت مکانیکی و سطحی مناسب هستند. در نتیجه تراشکاری سیلندر خارجی با کمک دستگاههای مدرن و ابزارهای پیشرفته، نقش اساسی در تولید قطعات دقیق و با کیفیت در عرصههای صنعتی دارد و به صورت مکرر در تولید انبوه و تولید قطعات خاص مورد استفاده قرار میگیرد. این فرآیند یکی از پایههای مهم در فرآیندهای تولید صنعتی محسوب میشود. همچنین بخوانید: تفاوت های بین تراشکاری […]
مقدمه برش فلزات، یکی از فرایندهایی است که در صنعت فلزات و ساخت و ساز مورد اجرا قرار می گیرد و می تواند به عنوان اولین مرحله در آغاز تولید یا ساخت قطعه یا محصول فلزی خاص شناخته شود. در برش دادن انواع فلزات با ضخامت و نوع مختلف، از روش ها و تکنیک های متعددی استفاده می شود تا بتوان هدف نهایی از برش را به بهترین شکل ممکن به دست آورد. در این مقاله با معرفی روش های مختلف و رایج برق فلزات، شما را با این فرایند مهم از صنعت فلزات آشنا می سازیم. با سری تراشی همراه باشید. برشکاری فلزات چیست و چه کاربردی دارد؟ هدف از برشکاری فلزات، به دست آوردن اندازه و شکل معینی از یک قطعه فلز می باشد. حال این قطعه فلزی می تواند با توجه به ضخامت، نوع و کاربردی که دارد، با استفاده از روش ها و شیوه های معمول یا اختصاصی برشکاری، مورد برش قرار بگیرد تا به شکل تعیین شده تبدیل شود. در درجه اول، فلزات از نظر نوع و در درجه دوم از نظر ضخامت با یکدیگر متفاوت می باشند. به همین دلیل کاربرد استفاده از هر یک با توجه به این موارد، متفاوت است. ممکن است یک قطعه فلزی که برای ساخت یک دستگاه تجهیزاتی خاص برش داده می شود، از یک روش حرارتی برای برشکاری استفاده کند. اما آن فلز در صورت استفاده در تولید یک محصول دیگر، با روش معمولی و سرد برش داده شود. بنابراین نوع استفاده از فلز و اهداف آن نیز می تواند در نوع برش و روش آن موثر باشد. به طور کلی در صنایعی مانند پتروشیمی، ساختمان سازی، خودروسازی و… از فلزاتی با انواع و ضخامت مختلف استفاده می شود که هر یک باید براساس نوع نیاز و اهدافی که دارند، در اشکال و ضخامت های مختلف با شیوه ای خاص برش بخورند. در اجرای برشکاری فلزات، ضمن انتخاب روش و ابزار مناسب برای این کار، باید نکات ایمنی نیز مورد توجه قرار بگیرد تا فرآیند برشکاری در ایمن ترین شرایط برای اپراتور برشکار و فلز موردنظر به اتمام برسد. همچنین بخوانید: تراشکاری معرفی روش های مختلف برش فلزات برشکاری فلزات از نظر میزان دمای فلز در هنگام اجرای برش، به دو دسته برشکاری گرم و برشکاری سرد تقسیم می شود. به طور معمول در هر یک از این روش ها، از تکنیک و شیوه های متغیری براساس نوع فلز و نوع برش اعمال شده استفاده می شود که توسط اپراتور مورد ارزیابی و انتخاب قرار می گیرد و سپس در بهترین شرایط ممکن ار نظر تجهیزات و ایمنی، برشکاری موردنظر اجرا می گردد. در برشکاری گرم، فلز موردنظر که بیشتر از 02/0 درصد کربن دارد، توسط حرارت دهی به نقطه دمای بالایی می رسد که در این حالت با استفاده از ابزارهای دستی یا ماشینی برش موردنظر انجام می گیرد. از تکنیک های اعمال شده در برشکاری گرم می توان به برش هواگاز، برش لیزری، برش پلاسما، برش CNC، برش سنگ فرز، برش الکترودی و دیسکی آتشی اشاره کرد. در برشکاری سرد از حرارت استفاده نمی شود و صرفا استفاده از تجهیزات برش، در این فرایند صورت می گیرد. فلزاتی که سختی کمتری دارند و میزان کربن آن ها کمتر از 02/0 درصد است، امکان برشکاری با این روش را دارا هستند. از جمله تکنیک های اجرا شده در این روش می توان به روش واترجت، اره دیسکی، اره نواری و همچنین سنگ فرز اشاره کرد که همواره با استفاده از تجهیزات و فناوری های خاص اجرایی می شوند. اگر از لحاظ نحوه اجرای برش فلزات، تقسیم بندی صورت بگیرد، این فرایند به دو دسته برش مکانیکی و برش دستی نیز تقسیم می شود. در برش دستی، طبیعتا استفاده از روش های سنتی و بدون تجهیزات برقی انجام می گیرد اما در برش ماشینی، تجهیزات مدرن با فناوری پیشرفته در راس انجام این کار قرار دارند. برش دستی فلزات: تکنیک ها و کاربردها در مواقعی که نیاز به استفاده از تجهیزات و ابزارهای برش برای برشکاری فلز موردنظر وجود ندارد، می توان از ابزارهای برش ساده نظیر اره و پانچ، برای بریدن فلزات استفاده کرد. در این روش، قطعه فلزی به راحتی تحت اختیار اپراتور قرار می گیرد و برش های نواری، صاف یا منحنی روی آن اجرا می گردد. اره دستی، قیچی ورق بر دستی، قیچی اهرمی و سنگ فرز دستی از اصلی ترین ابزارهای برش دستی فلزات می باشند که براساس نوع نیاز، مورد استفاده قرار می گیرند. طبیعتا استفاده از ابزارهای دستی برای بریدن فلزات، زمان بالا و ایمنی زیادی را می طلبد. لذا لازم است اپراتور با رعایت نکات ایمنی نظیر استفاده از عینک، ماسک و دستکش ایمنی، شرایط کار مطلوبی را برای اجرای این روش فراهم آورد. از تکنیک های برش دستی فلزات در مواقعی که فلز موردنظر از ضخامت و سختی کمتری برخوردار است و همچنین حجم و اندازه برش روی فلز حداقل می باشد، استفاده می گردد. در واقع استفاده از این روش برای شرایط ذکر شده، می تواند در کاهش هزینه نیز موثر باشد. همچنین بخوانید: آشنایی با انواع ابزارهای تراشکاری برش ماشینی فلزات: روش های رایج صنعتی امروزه تعدد بالایی در تجهیزات و ماشین های برش فلزات وجود دارد که می تواند ضمن ایجاد برشی دقیق و سریع، امنیت شرایط کار را نیز برای اپراتورها ایجاد نماید. استفاده از روش ماشینی، صرفا برای فلزاتی استفاده می شود که امکان برش دستی آن ها وجود ندارد و یا در صورت امکان، اتلاف وقت و عدم تمیزی محل برش را ایجاد می کند. برش ماشین ی فلزات با روش های زیر اجرایی می شوند که معمولا ضمن داشتن تفاوت فاحش در نحوه اجرا و تجهیزات مصرفی، از هزینه متغیری نیز برخوردار هستند. برش لیزری تجهیزات لیزری که برای برش فلزات استفاده می شوند، به واسطه حرارت ساطع شده از نور لیزر روی فلز، عملیات برشکاری را بدون ایجاد تراشه انجام می دهند. سرعت و دقت برش این تجهیزات فوق العاده می باشد و می توانند فلزات را با ضخامت حداکثر 20 میل، در سرعت و ظرافت بالا مورد برش قرار دهند. برش CNC یکی از جدیدترین و بهترین روش هایی که برای برش فلزات استفاده می شود، برش CNC می […]
مقدمه دستگاه برش لیزری ابزاری دقیق برای برش و حکاکی روی مواد مختلف مانند چوب، فلز، پلکسی، چرم و پلاستیک است. برای استفاده صحیح از این دستگاه، ابتدا باید فایل طراحی موردنظر را در یکی از نرمافزارهای گرافیکی مانند CorelDraw یا AutoCAD آماده کرده و آن را با فرمت مناسب معمولاً DXF یا PDF به نرمافزار کنترل دستگاه منتقل کرد. گام بعدی تنظیم دستگاه است؛ این شامل انتخاب نوع ماده، ضخامت آن و تنظیم توان و سرعت لیزر بر اساس نوع کار است. برای مثال، برش پلکسی با ضخامت ۳ میلیمتر به توان و سرعت خاصی نیاز دارد تا لبهها نسوزند. پیش از آغاز برش، حتماً باید فاصله کانونی لنز (فوکوس) تنظیم شود تا لیزر با بیشترین دقت عمل کند. در ادامه باید ماده مورد نظر را روی میز دستگاه فیکس کرد تا در حین برش جابجا نشود. سپس عملیات تست یا Dry Run انجام میشود تا از درستی مسیر برش اطمینان حاصل گردد. در نهایت، با زدن دکمه شروع، عملیات برش آغاز میشود. استفاده از تجهیزات ایمنی مانند عینک محافظ، تهویه مناسب و مراقبت از خطرات آتشسوزی در حین کار با دستگاه الزامی است. چگونگی انجام عملیات برش لیزری و گامهای اجرایی آن عملیات برش لیزری شامل مراحلی دقیق و فنی است که با آمادهسازی طراحی شروع میشود. در ابتدا، طرح مورد نظر با استفاده از نرمافزارهای طراحی دو بعدی یا سهبعدی آماده میشود. این طرح باید دقیق باشد تا لبههای برش تمیز و بدون خطا باشند. در مرحله بعد تنظیمات دستگاه انجام میشود که شامل انتخاب توان لیزر، سرعت حرکت نازل و نوع گاز کمکی معمولاً اکسیژن یا نیتروژن است. این پارامترها بسته به جنس و ضخامت ماده تغییر میکنند. سپس لنز دستگاه تنظیم میشود تا فوکوس پرتو دقیقاً روی سطح ماده قرار گیرد. فاصله صحیح بین لنز و سطح ماده تأثیر زیادی بر کیفیت برش دارد. پس از تنظیم کامل، ماده روی میز دستگاه قرار گرفته و بهطور کامل ثابت میشود. یک مرحله تست انجام میشود تا از صحت تنظیمات اطمینان حاصل گردد. سپس عملیات برش آغاز میشود. پرتو لیزر با دمای بسیار بالا ماده را ذوب یا تبخیر میکند و با حرکت نازل، مسیر برش شکل میگیرد. در پایان قطعه برش خورده از ماده جدا شده و کیفیت لبهها بررسی میشود. در صورت نیاز، عملیات تکمیلی مانند پولیش یا تمیزکاری انجام میگیرد. همچنین بخوانید: تراشکاری فرآیند تولید اشعه لیزر در دستگاههای برش اشعه لیزر در دستگاههای برش لیزری از طریق یک منبع انرژی خاص تولید میشود که میتواند گازی مانند CO2، حالت جامد مانند فیبر یا دیودی باشد. فرآیند تولید لیزر با تحریک یک محیط فعال آغاز میشود. این محیط میتواند گاز، کریستال یا فیبر نوری باشد که با انرژی الکتریکی یا نوری برانگیخته میشود. با این تحریک، الکترونهای موجود در اتمها به سطوح انرژی بالاتر منتقل میشوند. هنگامی که این الکترونها به حالت پایه بازمیگردند، فوتونهایی آزاد میکنند. این فوتونها به نوبه خود سایر الکترونها را تحریک کرده و زنجیرهای از تابش نوری هماهنگ بهوجود میآورند. درون محفظه تشدید لیزر این فوتونها بین دو آینه بازتاب پیدا میکنند. یکی از این آینهها نیمهشفاف است و اجازه میدهد بخشی از نور تقویتشده به بیرون منتشر شود. این نور خروجی همان اشعه لیزری است که دارای تمرکز بالا، تکرنگی و همجهتی بینظیری است. پس از تولید، این اشعه به وسیله لنزها و آینههای دستگاه متمرکز شده و بر سطح ماده هدایت میشود. دمای بسیار بالای نقطه تمرکز، باعث ذوب یا تبخیر ماده شده و فرآیند برش را ممکن میسازد. کنترل دقیق اشعه از طریق نرمافزار انجام میشود تا الگوهای مورد نظر با دقت بالا پیادهسازی شوند. چگونگی هدایت اشعه لیزر به سمت لنز خروجی پس از تولید اشعه لیزر در منبع، این پرتو باید بهصورت دقیق به لنز خروجی منتقل شود تا بتواند عملیات برش را انجام دهد. این انتقال از طریق مجموعهای از آینهها و مسیرهای نوری داخل دستگاه انجام میشود. معمولاً دستگاههای برش لیزری دارای سه آینه اصلی هستند که اشعه را به شکل انعکاسی از منبع به سمت سر برش هدایت میکنند. این آینهها در مکانهایی ثابت قرار دارند و باید بهطور دقیق تنظیم شوند تا پرتو لیزر دقیقاً به مرکز لنز متمرکز شود. هرگونه خطا در زاویه آینهها باعث افت کیفیت برش یا حتی آسیب به لنز میشود. در نهایت اشعه پس از طی مسیر مشخص به سر برش میرسد، جایی که یک لنز مخصوص پرتو را جمع کرده و روی نقطه بسیار کوچکی روی ماده متمرکز میکند. این تمرکز باعث افزایش دما در آن نقطه شده و ماده را برش میدهد. نگهداری درست از آینهها و لنزها و تمیز بودن مسیر نوری برای دقت و عملکرد مناسب دستگاه بسیار حیاتی است. همچنین بخوانید: آشنایی با انواع ابزارهای تراشکاری تمرکزدهی پرتو لیزری برای دقت بالاتر در برش تمرکزدهی یا فوکوس کردن پرتو لیزری یکی از مهمترین عوامل در کیفیت برش لیزری است. این فرآیند باعث میشود پرتو لیزر روی یک نقطه بسیار کوچک متمرکز شود و دمای بسیار بالایی در آن نقطه ایجاد گردد. لنز موجود در سر برش نقش اصلی را در این تمرکز ایفا میکند. با تنظیم صحیح فاصله بین لنز و سطح ماده، پرتو دقیقاً روی سطح یا داخل ماده متمرکز میشود. این فاصله معمولاً با کمک ابزارهای مخصوص یا به صورت دستی تنظیم میشود. اگر فوکوس بهدرستی انجام نشود، پرتو پخش شده و باعث برش ناقص، لبههای ذوبشده یا کاهش سرعت برش میشود. در برخی دستگاهها، سیستم فوکوس خودکار (Auto Focus) وجود دارد که کاربر را از تنظیم دستی بینیاز میکند. تمرکز دقیق پرتو لیزر نه تنها کیفیت برش را افزایش میدهد بلکه مصرف انرژی را نیز بهینه کرده و زمان اجرای عملیات را کاهش میدهد. همچنین، در عملیات حکاکی، فوکوس صحیح باعث ایجاد جزئیات ظریفتر و تمیزتر میشود. مراحل تمیز کردن و پاکسازی پس از عملیات برش لیزری پس از پایان عملیات برش لیزری، تمیزکاری و نگهداری دستگاه اهمیت زیادی دارد و باعث افزایش طول عمر آن و کیفیت کارهای بعدی میشود. اولین مرحله، خاموش کردن کامل دستگاه و اطمینان از خنک شدن بخشهای داخلی است. سپس سطح میز دستگاه بررسی و از باقیماندههای مواد مانند خاکستر، ذرات بریدهشده و گردوغبار پاکسازی میشود. برای این کار میتوان از جاروبرقی صنعتی یا برس نرم استفاده کرد. آینهها و […]
توانایی ها
- سری تراشی و انجام کلیه خدمات تراشکاری با دستگاه سری تراش تمام اتوماتیک
- سری تراشی انواع قطعات صنعتی، خودرویی، قطعه سازی و غیره تولید قطعات آلومینیوم، قطعات برنجی، قطعات آهنی
- تراشکاری و تولید قطعات سری تراشی با سی ان سی CNC و فرز انواع قطعات برنجی، آلومینیوم، آهنی
- تراشکاری و انجام کلیه خدمات سری کاری، قطعه سازی و صنعتی آماده همکاری با صنعت کاران و شرکت ها