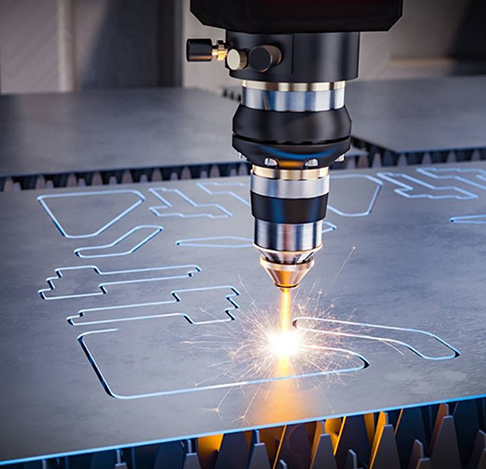
درباره ما
سری تراشی کریمان
با پیشینه افزون بر 4 دهه فعالیت موفق و حرفه ای و بهره مندی از نیروی انسانی متخصص و کارآمد ,تحقق ارزشهای مورد انتظار مشتریان را سرلوحه فعالیت خود قرار داده و امکانات و دستگاه های تمام اتوماتیک سریتراشی و سی ان سی و از تجهیزات پیشرفته و به روز جهت تولید قطعات مورد نیاز کارخانجات جهت تولید قطعات مورد نیاز با آلیاژ برنج آلومینیوم آهن از قطر دو تا شصت میلیمتر مطابق با معیارهای مورد انتظار مشتریان در خدمت صنعت کشور میباشد…
خدمات
شرح دستگاه و توانایی های این واحد صنعتی
دستگاه تراش سی ان سی CNC
سری تراشی با تراش cnc یک فرایند پیشرفته و کاربردی برای صنایع مختلف است. دستگاه تراش cnc ترکیبی از اعداد و کدها را اجرا می کند و با توجه به اینکه عملکرد دستگاه خودکار است در نتیجه موجب افزایش سرعت و دقت در تولید قطعات می شود.این دستگاه قادر است تا یک فرایند دستوری را برای دفعات زیادی به صورت دقیق اجرا کند.
تراش CNC از صنعت پزشکی گرفته تا صنایع خودروسازی و هوافضا کاربردی است. سری تراشی با تراش CNC در صنعت قطعه سازی جهان مدرن کاربرد ویژه ای دارد. این دستگاه قادر است کوچکترین قطعات را با دقت میکرون برش دهد.
دستگاه قلاویز زنی و حدیده کاری
قلاویز زنی یکی از جمله عملیاتی است که نیازمند دقت بالا در چرخش مته و سه نظام است. عمل قلاویز زدن بدون دستگاه های بادقت و با دریلهای معمولی کاملا غیر ممکن خواهد بود. دقت و قدرت بیشتر از مزایای مهم در دستگاه های تراشکاری کریمان میباشد که باعث محبوبیت و مورد توجه قرار گرفتن آن شده است. در نهایت و به عبارت بهتر، برای هر پروژه و قطعه کاری که نیازمند سوراخکاری دقیق، بدون هیچ انحراف و خطایی است و باید تمرکز در کارگیر و همچنین میزان فشار مته بر روی قطعه کاملا در اختیار کاربر باشد.که این امر نیز در مجموعه ما با دقت و سرعت بالا در حال انجام می باشد.
دستگاه های تراش تراب
دستگاه سری تراش یا تراب دستگاهی است که می تواند قطعات صنعتی قابل ماشین کاری را به طور سری و در تیراژ بالا تولید کند که به دلیل تولید اقتصادی با دقت و کیفیت بالا دستگاه تراش را در فرمها و شکلهای مختلفی میسازند و از طرفی به منظور ارزان بودن و سرعت بالای تراشکاری نسبت به سایر روشها استفاده از ماشین تراش یک روش معمول و پر استفاده در صنعت میباشد. لازم به ذکر است که تنظیم و راه اندازی این دستگاه مستلزم مهارت و تخصص خاصی میباشد تا در بازه زمانی معین به حداکثر تعداد تولیدات باکیفیت دست یافت که خوشبختانه مجموعه تراشکاری کریمان با به کارگیری نیروهای متخصص و مجرب در این زمینه زیرساخت های لازم جهت تولید قطعات با کیفیت با سرعت و دقت مثال زدنی را فراهم ساخته است.
مقالات
آخرین مقالات
دستگاه های سری تراش، ماشین آلات صنعتی تراش برای تراشکاری انواع قطعات فلزی، چوبی و پلاستیکی هستند که اغلب قطعات را در شکل های دوار و مخروطی، در نوع رزوه دار و ساده (پیچ و… ) تراش می دهند و قطعه موردنیاز برای ساخت یک محصول فلزی و غیرفلزی را تولید می کنند. با توجه به نیاز تولید، نوع قطعه خام، نحوه تراش و شکل نهایی محصول و همچنین نحوه عملکرد ماشین آلات، دستگاه های سری تراش در انواع گوناگونی به تولید می رسند که لازم است برای استفاده راحت و اصولی از آن ها، نوع مناسبی از ماشین آلات سری تراش را انتخاب نمود. این دستگاه در سه دسته اصلی دستگاه تراش دستی، نیمه اتوماتیک و تمام اتوماتیک تقسیم می شود که کارکرد و مدل های هر یک متفاوت است. در صفحه مجموعه سری تراشی کریمان، اطلاعات جامعی از این دستگاه را در اختیار شما قرار می دهد. دستگاه سری تراش دستی چیست؟ اولین و به اصطلاح قدیمی ترین دستگاه سری تراش برای تراشیدن قطعات خام به حول محور خود، نوع دستی دستگاه سری تراش می باشد. بیشترین میزان کارکرد این محصول برای تراش دادن قطعه خام فلزی و غیرفلزی، توسط اپراتور استفاده می شود و به اصطلاح هدایت عملکردی صفر تا صد دستگاه، توسط اپراتور صورت می گیرد. این دستگاه ها دارای ابزار نگهدارنده هستند که امکان نصب ابزارهای تراشکاری روی آن ها در نوع تکی و چندتایی وجود دارد. برجک این دستگاه نیز کاملا در اختیار اپراتور قرار دارد و با کنترل و چرخاندن آن توسط اپراتور، می توان تراش لازم را توسط ابزارها روی قطعه خام موردنظر انجام داد. مزایای دستگاه سری تراش دستی این محصول به سبب اینکه توسط اپراتور هدایت و کنترل می شود، بیشتر برای صنعت گران محبوبیت ندارد اما مزایای کار با این دستگاه سری تراش نیز در نوع خود قابل توجه است که در ادامه ببان می کنیم: هزینه پایین دستگاه این محصول به علت نداشتن یک سری قطعات حرفه ای با عملکرد خودکار، نیاز به تعمیر و سرویس دوره ای با هزینه بالا ندارد و صرفا با فرسودگی و با شکستن بخشی از قطعات، به تعویض یا تعمیر نیاز پیدا می کند. بنابراین نسبت به مدل های یگر این محصول از هزینه نگهداری فوق العاده پایینی برخوردار است. سادگی عملکرد دستگاه سری تراش دستی، از کارکرد فوق العاده آسان و ساده ای برخوردار است که در بسیاری از مواقع امکان تراش دلخواه قطعه را با کنترل کامل اپراتور انجام می دهد. معایب سری تراش دستی موارد مهمی که میزان خرید و استفاده از این محصول را در حال حاضر کاهش می دهد، معایبی است که در ادامه به آن اشاره می کنیم:. نیاز به اپراتور ماهر تراشکاری قطعه خام با این دستگاه، تحت کنترل اپراتور صورت می گیرد بنابراین نیاز است اپراتور کاملا بر نحوه تراشکاری مسلط باشد و با استفاده از تخصص خود، این کار را به صورت حرفه ای اجرایی نماید. زمان بر بودن به علت دستی بودن عملیات تراشکاری روی قطعه خام موردنظر، بالطبع زمان آجرای این روش بیشتر از زمان استفاده از دستگاه های نیمه اتوماتیک و اتوماتیک می باشد. موارد کاربردی دستگاه های دستی در تولیدات محدود به طور کلی تولید قطعات خاص و کوچک که نیاز به تراشکاری با دستگاه های سری تراش دارند و از حجم کم و بودجه محدود دارا می باشند، نیاز است از ماشین الات دستی سری تراشی استفاده کنند که این مورد در انواع صنایع مانند تولید قطعات موردنیاز برای صنایع چوبی و لوازم خانگی مناسب است. همچنین بخوانید: نقش سری تراشی دقیق در تولید قطعات با استانداردهای صنعتی دستگاه سری تراش نیمه اتوماتیک یکی از کاربردی ترین دستگاه هایی که عملیات تراشکاری سطحی را با عمق مختلف روی قطعات خام فلزی و غیر فلزی انجام می دهد، دستگاه نیمه اتوماتیک سری تراشی می باشد که همانند عنوانی که دارد، کارکرد نیمه اتوماتیک دارد و بخشی از اجرای تراشکاری را به صورت خودکار انجام می دهد و بخشی دیگر را به اوپراتور واگذار می کند. تفاوت با مدل دستی این محصول بخش مهمی از مسئولیت کنترل و هدایت ابزارها و برجک را توسط اوپراتور کاهش می دهد و می تواند به صورت خودکار و بدون نیاز به اوپراتور، تراشکاری را انجام دهد که این امر تنها تفاوت عملکردی آن با دستگاه دستی سری تراش به شمار می رود. اما به علت ساختار نیمه اتوماتیک، برای اجرای عملیات به کنترل اپراتور نیز نیاز ضروری دارد تا عملیات خودکار را تحت نظر فرد انجام دهد. اجزای کنترل مکانیکی یا پنوماتیکی دو سیستم مهم برای عملکرد این دستگاه با عناوین “سیستم مکانیکی” و “سیستم هیدرولیکی” استفاده شده اند که می توانند عملیات مکانیکی و یا اتوماتیک محصول را انجام دهند. اجزای مکانیکی این دستگاه برای کنترل کردن راحت تر اپراتور استفاده می شود و اجزای هیدرولیکی نیز جهت اجرای راحت عملیات خودکار و اتوماتیک به کار می رود. از جمله اجزای سیستم پنوماتیکی (مکانیکی) می توان به موارد زیر اشاره کرد: شیر کنترل برای کنترل کردن جریان هوا سیلندرها برای تامین نیرو برای حرکت اجزای مکانیکی دستگاه رگلاتور برای تنظیم فشار هوا روغن زن برای روغن کاری قطعات متحرک ماشین مزایای دستگاه سری تراش نیمه اتوماتیک با توجه به کاربرد مناسب این ماشین در صنعت سری تراشی، مزایایی که با بهره گیری از آن، متوجه صنعت موردنظر می شود به قرار زیر هستند: دقت بالا در تراشکاری در عمق متغیر به علت بهره گیری از اجرای خودکار تراشکاری، این دستگاه می تواند جزئیات بالاتری از تراش را روی قطعه موردنظر پیاده کند که در دستگاه های دستی، اجرای آن سخت و یا غیرممکن بود. کاهش نیاز به نیروی انسانی با منتقل شدن اجرای بخشی از عملیات تراش این می گیرد به سیستم اتوماتیک، نیازی به استفاده از تخصص و تجربه اپراتورها نیست و صرفا برای کنترل و هدایت بخشی از راندمان این دستگاه، از تعداد معدودی اپراتور استفاده می شود. معایب سری تراش نیمه اتوماتیک این دستگاه با داشتن کارکرد قابل توجه، نیاز به تعمیرات بیشتری نسبت به مدل دستی دارد که صرفا جهت اجرای عملکرد بی نقص ضروری می باشد. لذا هزینه نگهداری این محصول نسبت به نوع دستی بیشتر می باشد. کاربرد در صنایع متوسط یا نیمه انبوه با […]
سری تراشی به عنوان یکی از فرایندهای قابل توجه در صنایع تولیدی قطعات فلزی و غیرفلزی، نقش مهمی در صنعت تولید دارد اما با توجه به نوع فعالیت و عملکردی که دارد، تفاوت بسیار زیادی با عملکرد دستگاه CNC دارا می باشد. مجموعه سری تراشی کریمان در این صفحه با ارائه اطلاعات کامل درباره سری تراشی و CNC، شناخت کلی ابزار و عملکرد این دو روش را ارائه می کند. معرفی کلی تراشکاری و اهمیت روش های مختلف آن تراشکاری یکی از مهمترین مراحل تولید قطعات فلزی و غیرفلزی می باشد که به واسطه آن، مواد خام فلزی و غیرفلزی (چوبی، استیل، آلومینیوم و… ) در قطعات مختلف، توسط دستگاه ها و فرآیندهای خاص تراش می خورند تا شکل نهایی قطعه موردنظر به دست آید. در تراشکاری عموما از قطعه خام به صورت مکعبی، استوانه ای و.. استفاده می شود و این امر بستگی به نوع و شکل قطعه نهایی دارد که در راستای تراشکاری، باید به طراحی و تولید برسد. برداشتن لایه های سطحی قطعه خام در عمق مختلف و یکپارچه کردن سطح آن، جزو اصلی ترین اهداف این فعالیت می باشد. لذا قطعه خام در جنس، اشکال و وزن مختلف برای تبدیل به شدن به یک قطعه با شکل خاص، مورد تراشکاری قرار می گیرند. این فرایند برای تولید انواع قطعات فلزی و غیرفلزی مصرفی در انواع صنایع بزرگ و کوچک استفاده می شود. تراشکاری در صنایع بزرگ برای تداوم فعالیت هواپیماسازی، خودروسازی، پزشکی، الکترونیک، محصولات چوبی و… بسیار اهمیت دارد که برای تولید قطعات موردنیاز هر یک از این صنایع، از روش های منحصر به فردی تراشکاری استفاده می شود. محصولاتی که به صورت خام یا آلیاژی نیاز به تراش دارند، توسط روش های مختلف مانند روش دستی، استفاده از دستگاه تراش و یا CNC تراشیده می شوند. انتخاب روش اجرایی برای این فرایند، طبیعتا نیاز به شناخت جنس و نوع قطعه نهایی کار دارد تا روش مناسب انتخاب شده و در کمترین زمان و بالاترین سرعت، قطعه نهایی با جزئیات کامل و کیفیت بالا تراش بخورد. خدمات سری تراشی سری تراشی چیست؟ یکی از شاخه های مهم در فرآیند تراشکاری، سری تراشی می باشد که به عنوان یک روش مجزا و اختصاصی، در این صنعت مورد استفاده قرار می گیرد. در سری تراشی، قطعه خام با قرارگیری روی محور اصلی، به دور خود می چرخد و ابزارهای تراش اعمال شده روی ماشین آلات تراش تمامی لایه های اضافی قطعه را برای رسیدن به شکل نهایی، در عمق متغیر تراش می دهد. در انجام فرآیند موردنظر، روش های مختلف تراشکاری براساس نوع و شکل قطعه استفاده می شوند. به طور کلی سری تراشی از لحاظ پیچیدگی قطعه نهایی و همچنین جزئیات تراش، دارای روش های مختلف اجرایی از ساده تا پیشرفته است. برای انجام هر یک از روش های سری تراشی، به یک یا چند اپراتور نیاز می باشد تا عملیات تراش را کاملا تحت کنترل خود قرار دهد و با تمرکز روی قطعه موردنظر و فرآیند اجرایی ابزارهای برش، به بررسی نحوه فعالیت و درستی آن بپردازد. انواع دستگاه سری تراشی با توجه به اطلاعات ارائه شده در بالا، برای استفاده از یک روش خاص برای تراش قطعه موردنظر، نیاز است تا روش اجرایی آن براساس پیچیدگی شکل قطعه نهایی و همچنین سرعت و جزئیات کار بررسی گردد. به طور کلی عملیات سری تراشی برای استفاده در صنایع مختلف، به قرار زیر می باشند: روش دستی در این روش، با بهره گیری از ابزارهای برقی و غیر برقی، قطعه موردنظر کاملا تحت اختیار اپراتور قرار می گیرد و فرد می تواند با بهره گیری از ابزارهای تراش و کنترل آن ها، تراش موردنظر را روی قطعه انجام دهد. طبیعتا به علت فعالیت کامل اپراتور و تسلط ویژه روی اجرای کار، سرعت و دقت به میزان زیادی کاهش پیدا می کند. لذا استفاده از آن برای قطعاتی با تعداد محدود و نیاز به تراش سطحی و ساده، مناسب است. لذا این قطعات می توانند با بهره گیری از روش تراشکاری دستی، هزینه کمتری را برای تراش داشته باشد. روش نیمه اتوماتیک در این روش، از دستگاه های تراشکاری خاص استفاده می شود که امکان دخالت اپراتور در فرآیند تراش را به نسبت روش دستی، بسیار کاهش می دهد و در نتیجه سرعت و کیفیت کار را بالا می برد. البته این روش، تسلط کامل اپراتور به نحوه اجرای فرآیند را نیاز دارد اما بیشترین فرآیند تراش توسط دستگاه انجام می گیرد. روش تمام اتوماتیک در این روش، از دستگاه های سری تراشی مدرن و کاملا اتوماتیک استفاده می شود که صفر تا صد عملیات تراش قطعه را تحت اختیار دارد و فقط به اپراتور امکان بررسی اجرای فرآیند و کنترل های سطحی را می دهد. این روش با توجه به اینکه نیاز به دستگاه های گران قیمت و حرفه ای دارد، هزینه تولید را بسیار بالا می برد اما به رغم آن اجرای فعالیت، سریع تر و در زمان کمتری صورت می گیرد که یکی از نقاط قوت و مثبت این امر می باشد. سیستم سی ان سی (ترکیبی) از مدرن ترین روش های اجرایی سری تراشی است که با بهره گیری از دستگاه CNC و سیستم منحصر به فرد آن اجرا می شود. این دستگاه با استفاده از یک سیستم کنترل گر، می تواند نحوه تراش را به صورت کامل و ریزبینانه توسط اپراتور دریافت کند و برنامه عملیاتی آن را روی قطعه بدون نیاز به کنترل اپراتور در مدت زمان بسیار کم و حجم بالا و تکراری انجام دهد. همچنین بخوانید: معرفی کامل ابزارهای کالیبراسیون دستگاه CNC تراشکاری CNC چیست؟ CNC یکی از مهمترین و حرفه ای ترین ماشین آلات تراش و برش است که قابلیت استفاده برای انواع قطعات با جنس مختلف را دارا می باشد و می تواند قطعه موردنظر را در هر شکل و حجم مورد تراشکاری، سوراخ کاری، پرداخت، شیارزنی، رزوه زنی و… قرار دهد. این محصول برای اجرای فعالیت تراش در صنعت سری تراشی اهمیت بسیار زیادی دارد و از آن در صنایعی که نیاز به تعداد بالایی قطعه تراشکاری شده با سرعت بالا وجود دارد، استفاده می شود. نحوه عملکرد دستگاه CNC از قابلیت های تراش این دستگاه، می توان برای تراش قطعات مختلف از جمله فلز استفاده […]
برای افزایش دقت عملکرد دستگاه های CNC مختلف، لازم است با فرایندها و سیستم های کالیبره خاص، برای کالیبره کردن آن اقدام کرد. این فرایند صرفا نیازمند آشنایی با ابزارهای کالیبراسیون دستگاه CNC و مراحل و چگونگی انجام کالیبره می باشد. سری تراشی کریمان در این مقاله، درباره چگونگی انجام این کار و ابزارهای دقیق و ضروری برای کالیبراسیون دستگاه های CNC اطلاعات جامعی را ارائه می دهد. ابزارهای مورد استفاده برای کالیبره کردن دستگاه CNC کدام اند؟ کالیبراسیون فرآیند افزایش دقت عملکردی انواع دستگاه های CNC می باشد که جزو مراحل نگهداری از این محصول نیز به شمار می رود. سیستم های کالیبره برای این دستگاه، با بهره گیری از ابزارهای خاص فعالیت می کند که این ابزارها باید به طور کامل از نظر کارایی و میزان نتیجه بخش بودن در فرآیند کالیبراسیون مورد بررسی قرار بگیرند. از انواع ابزارهای کالیبراسیون دستگاه CNC می توان به موارد زیر اشاره کرد: ساعت اندازه گیری سیستم توپ و ریل لیزر اینترفرومتر سیستم های پروپ سنسورهای دیجیتال و نرم افزارهای کالیبراسیون ابزار ساعت اندازه گیری یکی از مهمترین ابزارهایی که کالیبراسیون دستگاه CNC، ساعت اندازه گیری می باشد. این ابزار به علت تنظیم کردن انحراف و لنگی محورها و همچنین میز ماشین کاری، با این عنوان نامگذاری شده است. البته بیشترین استفاده از این محصول برای تنظیم کردن محور Z دستگاه استفاده می شود. آشنایی با سیستم Ballbar برای کالیبراسیون دقیق CNC یکی از کاربردی ترین ابزارهای کالیبراسیون دستگاه CNC، سیستم Ballbar می باشد که می تواند خطاهای هندسی و مکانیکی محور دستگاه CNC را با اندازه گیری دایره های اعمال شده توسط این محصول در طول فرآیند اجرایی، شناسایی کند. کاربرد لیزر اینترفرومتر (Laser Interferometer) در کالیبراسیون دستگاه CNC در این ابزار، با استفاده کردن از امواج نوری، تشخیص تغییر موقعیت زاویه های محور و همچنین فاصله و سرعت آن ها به صورت نانومتری امکان پذیر می شود. این ابزار دقت بسیار بالای نانومتری دارد و می تواند موقعیت تغییراتی را تشخیص داده و با بررسی میزان خطا، فایل جبران خطا را ارائه دهد تا به صورت خودکار، خطای موردنظر برطرف گردد. نقش پروب لمسی (Touch Probe) در فرآیند کالیبراسیون دستگاه های CNC این ابزار می تواند با اندازه گیری دقیق موقعیت میز کار با قطعه، مختصات آن را شناسایی کند و ابزارهای دارای خطا را تراز نمایند. خطاهای قابل شناسایی دستگاه CNC توسط این ابزار شامل خطای عمودی محورها، خطای صاف بودن میزکار و همچنین خطای انحراف یا موازی بودن ریل ها می باشد. استفاده از سنسورهای دیجیتال و نرم افزارهای تخصصی در کالیبراسیون CNC دستگاه CNC در نوع اتوماتیک می توانند به صورت حرفه ای و هوشمند در این فرایند نقش داشته باشند. یکی از هوشمندترین ابزارهای کالیبراسیون دستگاه CNC پیشرفته و حرفه ای، سنسورهای دیجیتالی و همچنین نرم افزارهای CAD/CAM است که با قابلیت تشخیص دادن تغییرات غیر طبیعی در حیطه دما، فشار، حرکت و… می تواند با ارائه دستورات تغییراتی، به رفع خطاهای موجود بپردازد. همچنین بخوانید: تراشکاری چیست؟ کالیبره کردن دستگاه CNC افرادی که سعی در کالیبراسیون کردن دستگاه خود با استفاده از ابزارهای کالیبراسیون دستگاه CNC می کنند، باید این کار را با توجه به نوع دستگاه CNC، ابزارهای مورد استفاده و همچنین نوع تولید و هدف موردنظر انجام دهند. در ادامه جزئیات بیشتری از مراحل گام به گامی این فرایند را ارائه می کنیم. مرحله اول: بررسی وضعیت کلی دستگاه CNC قبل از شروع کالیبراسیون انواع دستگاه CNC چوب یا فلز، باید قبل از کالیبره شدن، مشکلات موجود در آن از جانب برقی، نرم افزاری و همچنین مکانیکی مورد بررسی و شناخت قرار بگیرد. به عبارتی اگر دستگاه موردنظر از نظر قطعات فیزیکی خود دارای مشکلاتی نظیر شل شدن پیچ، خراب شدن بلبرینگ و… باشد، امکان موفقیت آمیز بودن کالیبره را بسیار پایین می آورد. از این رو بررسی تمامی این موارد و رفع خرابی و مشکلات مذکور در سیستم های فیزیکی، نرم افزاری و حتی اتصالات برق به عنوان اولین مرحله برای کالیبراسیون دستگاه به شمار می رود. مرحله دوم: تنظیم دمای محیط و آماده سازی گرمای اولیه دستگاه برای اینکه دستگاه CNC در هر نوعی شروع به فعالیت تولیدی کند، لازم است برای داشتن دقت بالا در برش، تراش و… دمای حرارتی مناسبی را داشته باشد که این امر با کار کردن به مدت نیم ساعت بعد از روشن شدن دستگاه صورت می گیرد. لذا برای کالیبراسیون دستگاه CNC نیز باید دمای مجاز برای محصول تامین شود که بهتر است حداقل نیم ساعت بعد از آغاز فعالیت آن، کالیبراسیون صورت بگیرد. مرحله سوم: انتخاب ابزار کالیبراسیون مناسب برای دقت بالا در این مرحله باید با بهره گیری از ابزارهای کالیبراسیون دستگاه CNC، اقدامات لازم برای اندازه گیری زاویه محورها و همچنین شناخت خطا و رفع آن انجام بگیرد. ابزارهای موردنیاز برای این کار نظیر Ballbar، اینترفرومتر، پروپ و… می باشند که آن ها انواع بررسی ها نظیر بررسی انواع انحراف در محورهای X، Y و Z، سنجش موقعیت صفر، بررسی اندازه انحراف های زاویه ای و همچنین صاف و مسطح بودن میز کار را انجام می دهند. مرحله چهارم: ثبت داده ها در نرم افزارهای CAD/CAM یا پلاگین های مرتبط برای اینکه نتیجه کالیبراسیون دستگاه CNC مورد مشاهده قرار بگیرد، اغلب از نرم افزارهای پلاگین CAD/CAM استفاده می شود. این نرم افزارها با دقت بالا، نتیجه بررسی ابزارهای کالیبراسیون دستگاه CNC را بیان می کنند. در صورتی که میزان خطای اعلام شده در نتایج موردنظر بیشتر باشد، می توان با تغییرات سیستمی، تنظیمات دستگاه CNC را برای رفع خطاها آماده کرد. مرحله پنجم: اعمال تنظیمات اصلاحی و تکرار تست جهت تایید صحت طبق خطاهای اعلامی از طریق نرم افزارهای سیستمی، اصلاحیه خطاها اعمال می شود. اما لازم است قبل از شروع به کار دستگاه CNC، یک تست از دستگاه گرفته شود تا تمامی اصلاحات انجام شده در کالیبراسیون، مورد تایید قرار بگیرد. همچنین بخوانید: مایع خنک کننده CNC چیست؟ مراحل گام به گام کالیبراسیون دستگاه CNC برای اینکه کالیبراسیون دستگاه به صورت عملی اجرایی شود، باید هر یک از مراحل بالا، با تکنیک های خاص مورد انجام قرار بگیرد. اما تکنیک های اجرایی هر یک از مراحل، مجزا و متفاوت می باشند که در ادامه هر یک از آن ها را […]
توانایی ها
- سری تراشی و انجام کلیه خدمات تراشکاری با دستگاه سری تراش تمام اتوماتیک
- سری تراشی انواع قطعات صنعتی، خودرویی، قطعه سازی و غیره تولید قطعات آلومینیوم، قطعات برنجی، قطعات آهنی
- تراشکاری و تولید قطعات سری تراشی با سی ان سی CNC و فرز انواع قطعات برنجی، آلومینیوم، آهنی
- تراشکاری و انجام کلیه خدمات سری کاری، قطعه سازی و صنعتی آماده همکاری با صنعت کاران و شرکت ها